Working in Chicago
July 25, 2023

This article was originally published in the July 1994 issue of DEMOLITION magazine, then called Demolition Age.
The Windy City is booming. The Chicago Opera House is being renovated, there is work on the Dan Ryan and Kenned Expressways, and O’Hare is always under construction. Over the past year, Chicago’s Brandenburg Industrial Service Co. has been involved with two of the largest demolition projects in the city: several buildings for the new McCormick Place expansion project and the Sears Catalogue Warehouse.
McCormick Place
The McCormick Place, Chicago’s convention center, job is part of a $654,000,000 expansion project that will add a 2.7-million-square-foot building that will connect two existing exhibition halls. Brandenburg has a demolition contract that will be done in two phases. The first phase was wrecking the 20-year-old, 27-story, 278-foot-tall McCormick Inn Hotel and the 3-story, 400,000-square-foot Donnelly Hall exhibition center, including all subgrade concrete. The second phase will start this fall and will include demolition of a commercial bank and the removal of the 23rd Street viaduct, an elevated, six-lane structure that ran between the hotel and the north exhibition hall, connecting them to Lake Shore Drive and the main McCormick Exhibition Hall.
Time was of the essence on the hotel project, as it had to be completely wrecked within 90 days. A liquidated damage penalty of $60,000 per day was definitely an incentive to finish on time. Brandenburg worked around the clock six days per week to meet the deadline. After the last guests checked out, hotel employees stayed until 8 p.m. that same day to remove the few items that were not included in the sale of the property and to have an employee farewell party. At the end of the party, a Brandenburg subcontracted minority moving firm began working seven days straight, around the clock to remove all the contents of the hotel. Brandenburg donated 600 rooms of mattresses and box springs, and 250 rooms of bedroom furniture to the United Way, which donated them to several local charities. The remainder of the contents were sold to National Contract Liquidators (NCL) of Dayton, Ohio. Both the local moving firm and NCL worked feverishly to meet the seven-day deadline allotted for the removal of contents.
As the contents were removed, Brandenburg’s laborers followed close behind removing all combustibles such as carpeting, vanities, etc. As soon as the contents were gone, electrical power was severed and a portable generator was brought in to power stairwell lighting and fire pumps.
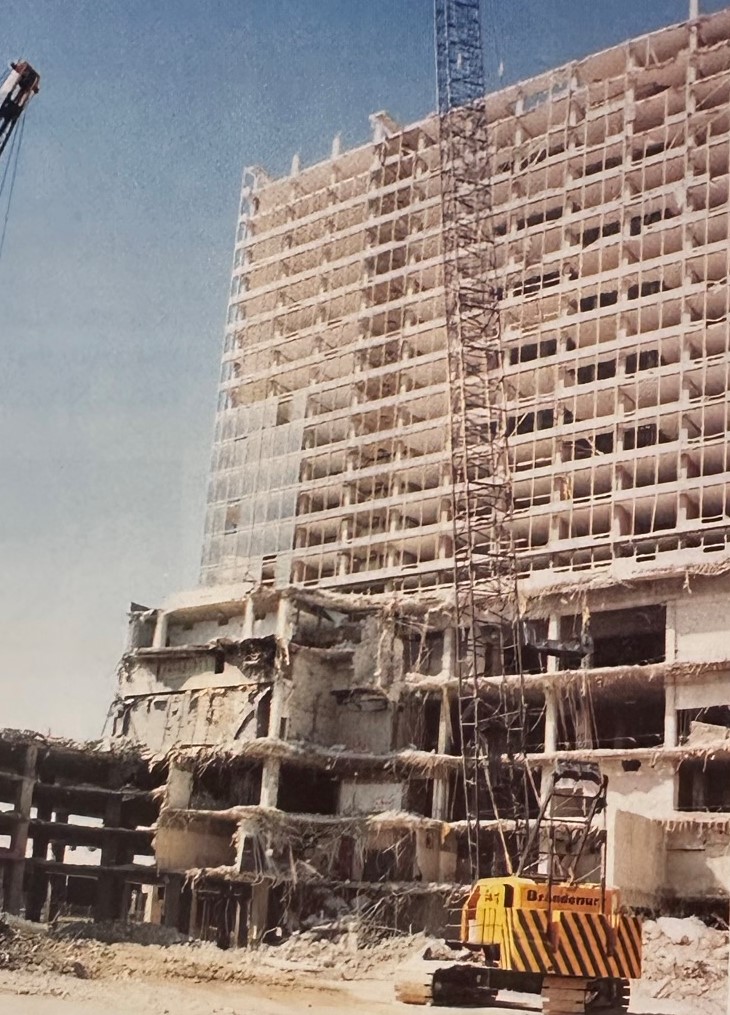
Two crawler cranes were then brought on-site; a 165 ton crane with 300 feet of boom and a 150 ton crane with 120 feet of boom. The larger crane was used to hoist up the 12 skid steer loaders that were used on the floors of the building and to bring the salvaged roof-mounted mechanical equipment to the ground. At the same time, the smaller crane began balling the adjacent 1-story parking garage. Aircraft warning lights had to be attached to the boom because of the proximity to Miegs Field, a commuter airport just across the street. Two rubber-tired front-end loaders and two excavators on the ground loaded trucks and crushed concrete within reach. Skid steer loaders were lowered floor by floor using steel ramps. Floors were reinforced from underneath with temporary supports to handle the weight of these loaders.
Brandenburg exceeded strict minority requirements. In addition to subcontracting furniture moving, trucking and electrical work, they also sold scrap to a minority dealer and rented equipment from a minority rental agency. They also hired several unskilled laborers from the neighborhood and trained them as demolition workers.
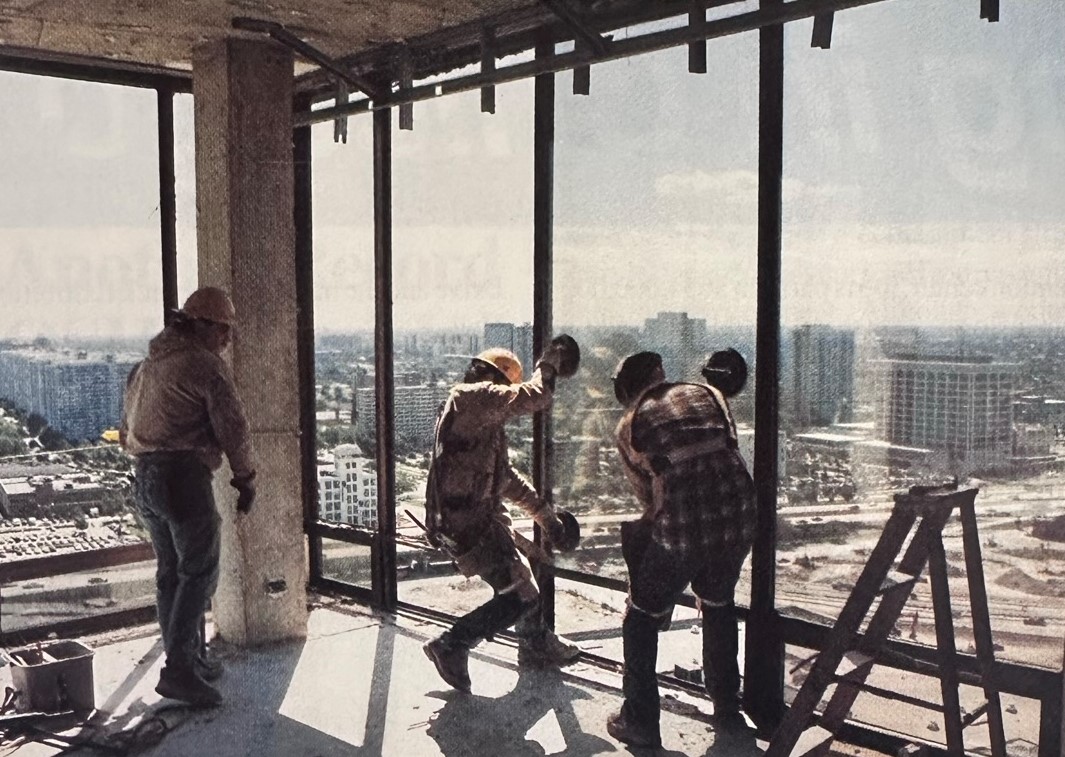
After finishing the hotel, a pedestrian tunnel that linked the hotel with Donnelly Hall, as well as over live electric commuter train tracks, was removed and demolition began on Donnelly Hall. Before becoming an exhibition hall, this building was a printing plant that was constructed with 18” thick concrete floors. Floors were balled and columns were broken with an excavator-mounted universal processor. Brandenburg used a crane, four excavators, a bulldozer with a ripper, and both track and rubber-tired loaders to complete the job.
Safety was a prime consideration on the project and was a significant criteria for the owner in choosing the demolition contractor. All buildings were surveyed and all possible potential accident situations were considered. Heavy pedestrian traffic from conventions in the two nearby exhibition halls and traffic along Chicago’s Lake Shore Drive immediately east of the hotel required special precautions, as the entire exterior of the building was glass. Brandenburg hired a glazing contractor who instructed its people in the safe removal of glass. In addition to the special hand tools required for removing the glass, the workers were outfitted with leather aprons, gauntlets and gloves.
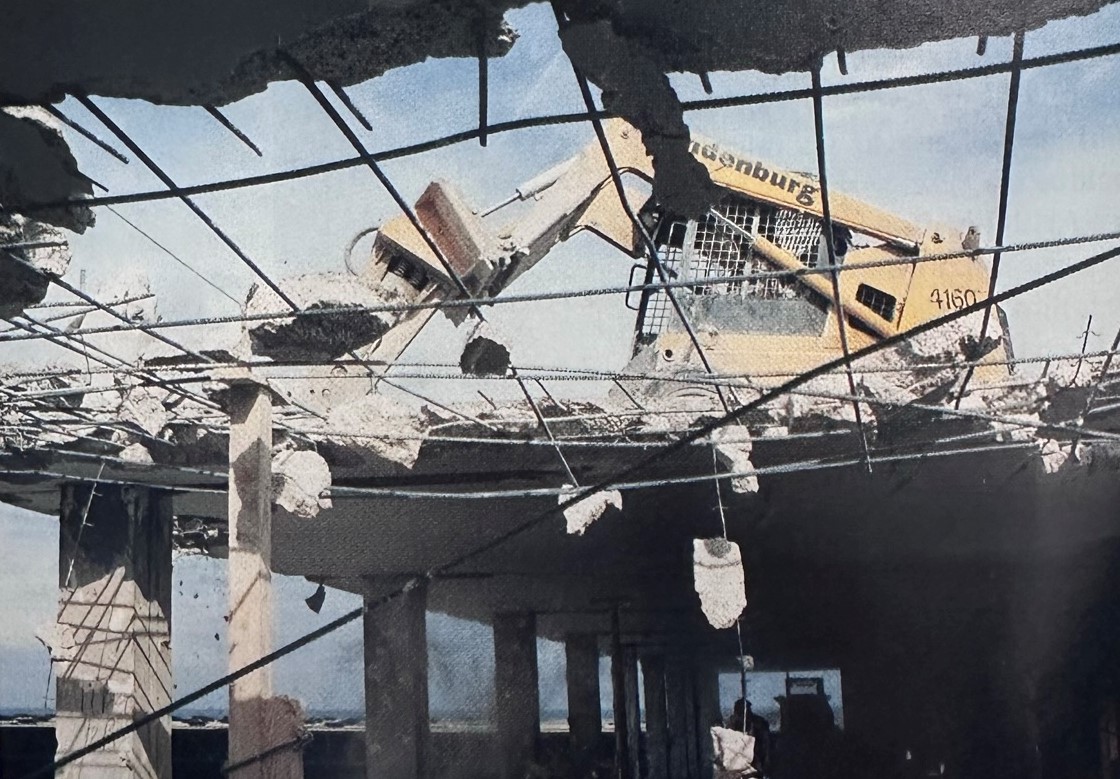
Two of the engineers laid off from the hotel were hired to help disconnect utilities. A full-time safety person was kept at the main entrance to the site to help trucks exit and to prevent taxi drivers, who insisted the hotel was still open, from entering.
Recycling was also an important part of this project. Several elevator shafts in the buildings were used separately as material chutes for glass, concrete, steel, nonferrous metals and debris. All concrete was sent to a nearby crusher and much of it will be returned to the new construction site as fill. All the freon was also recycled.
Sears Catalogue Warehouse Center
The demolition of the Sears Catalogue Warehouse on Chicago’s West Side will also keep Brandenburg busy, for almost a year. This is a 9-story, 3-million-square-foot brick and timber building built in 1906. It encompasses two city blocks and is being torn down to make way for 600 new apartments, townhomes and single-family houses. A 14-story click tower, a neighborhood landmark, and a 50’ area immediately around it will be saved and restored.
After abating the asbestos and 37,000 PCB containing ballasts, Brandenburg began wrecking the structure using a 165-ton crane with a clam bucket. Over 7.5 million board feet of yellow pine wood beams and decking will be recycled, as well as an estimated 23 million bricks. Interest in the wood has been worldwide, as this may be the largest wood frame building ever built.
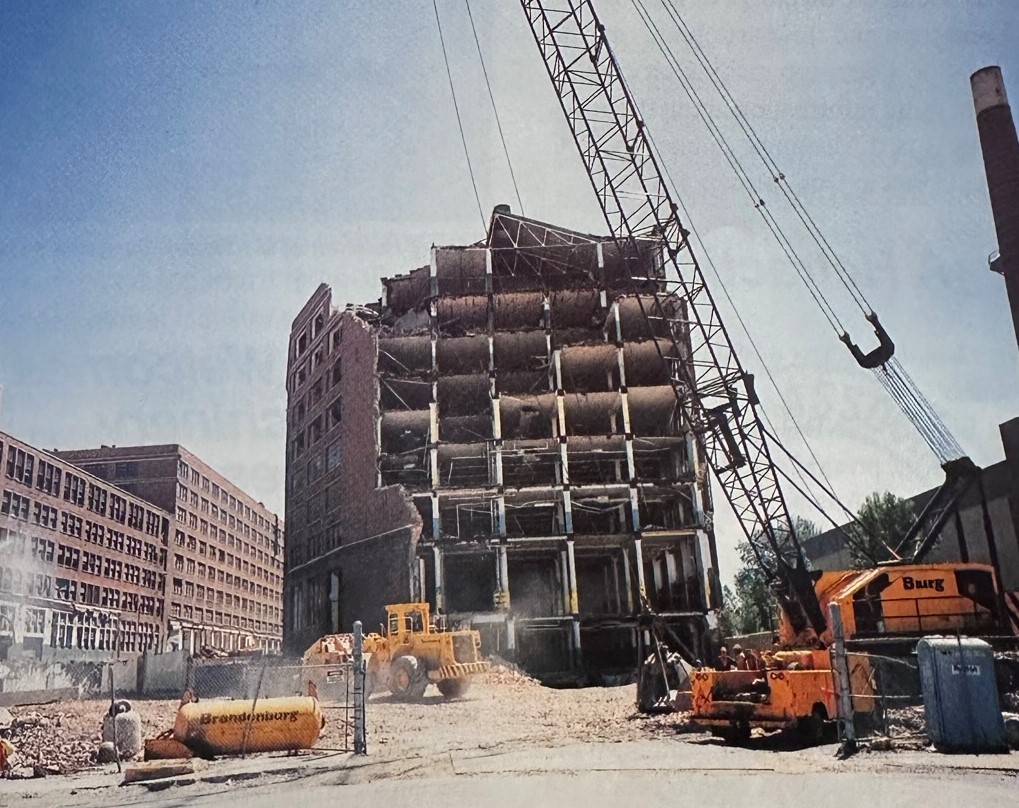
Although a private project, strict minority hiring requirements are in effect on this job. Again, Brandenburg has exceeded these goals by working with the local alderman’s office in the neighborhood to assist residents in the area. Meetings were held with local contractors to solicit bids for possible subcontracts.
Unskilled residents in the area were advanced tuition money to attend an asbestos training school and were put to work upon graduation. Several other unskilled workers are being trained as demolition workers. Brick and timber recyclers subcontracts will require a majority of employment from the neighborhood.
Safety on this job is also a prime consideration. Although the entire building is sprinklered, no more than 100 feet of any floor has its sprinkler system disconnected at any time. In areas where sprinklers are disconnected, fire hoses are connected to temporary water pumps. The entire site will be fenced at all times and a full-time safety person is assigned to the project.
Initially the Sears project had been delayed as the Historical Landmark Commission was evaluating the structure to determine if it was a historical landmark in the city of Chicago.