Controlling Indoor Demolition Dust
March 15, 2022
By: Rick Felde
A pioneer in atomized misting equipment has helped a demolition company protect workers and the surrounding community from potentially hazardous dust during indoor demolition with its newest suppression technology. As mini-excavators demolished the inside of a former mall, East Coast Demolition used the DustBoss Atom® for automated particle control. With no need for labor to hold a hose, the Atom prevented dust emissions from remaining airborne or leaving the area.
East Coast Demolition (ECD) is a full-service hazardous material abatement and demolition contractor serving northeastern North Carolina and Virginia. The firm was contracted to demolish, recycle, clear and prep the old site of The Village Shops at Kingsmill in Williamsburg, Virginia. Due to its proximity to residential communities and local businesses, the general contractor selected ECD for its experience in the proper handling of hazardous materials and dust suppression methods.
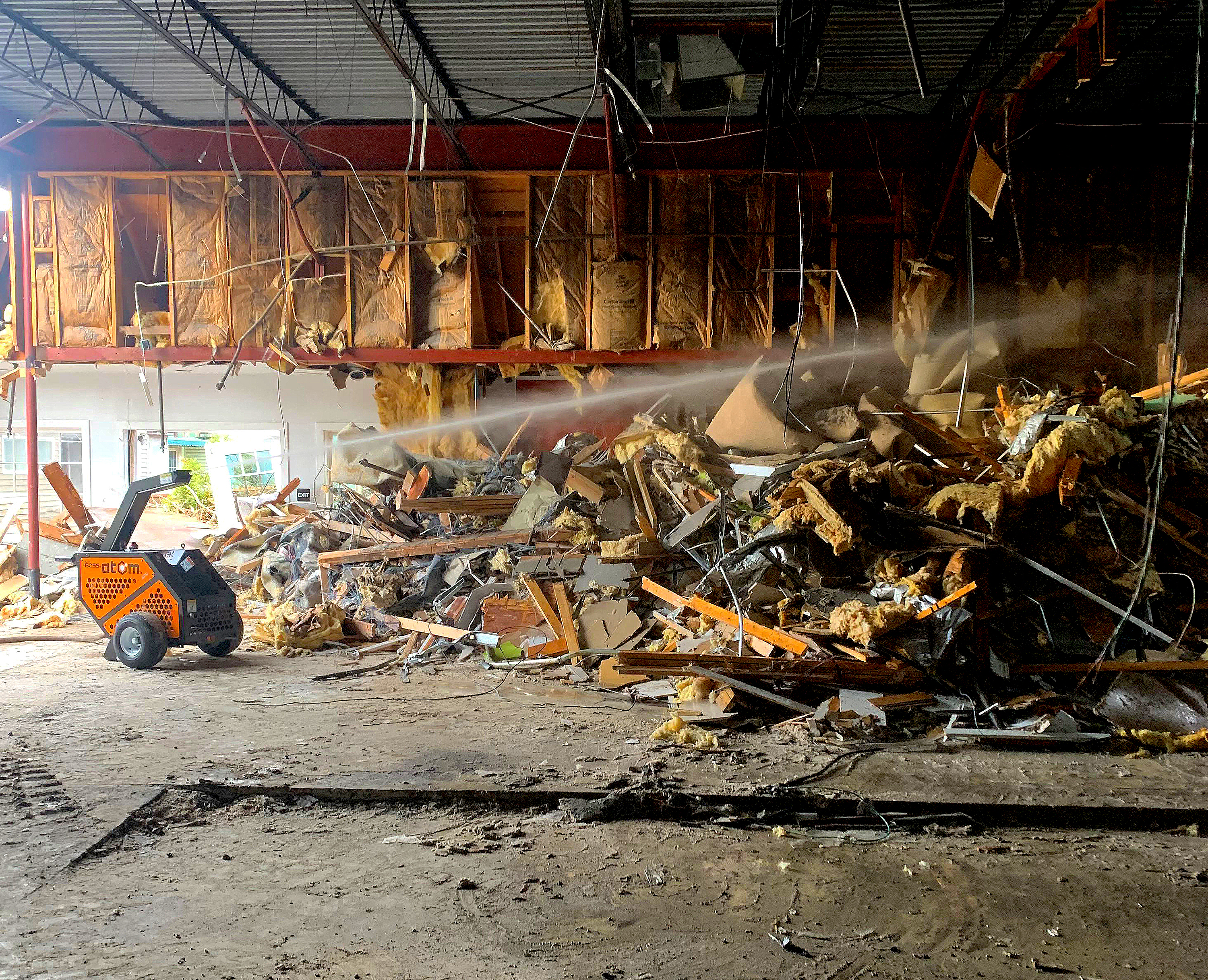
DustBoss Atom performs indoor suppression during the soft-stripping process.
“Owners, general contractors and developers select East Coast because we offer worry-free, turnkey services,” says Ricky Webb, chief operating officer of East Coast Demolition. “We initiate, perform and execute projects of all sizes and complexities for the private, municipal, commercial and federal markets. We take environmental hazards very seriously, because we want to be good stewards of the communities we serve. From a best practices standpoint, experience has taught us that atomized misting equipment for dust suppression is one of the best safety and compliance tools in our fleet.”
The project involved the demolition of seven structures with a total of approximately 81,000 square feet of building space and more than 4 acres of asphalt flattop. The estimated timeline was 10-12 weeks to take down structures made primarily of cinder block and brick on a cement foundation. Using a fleet of 12 dump trailers, the site prep involved a complete clearing of all debris with the exception of crushing stone material into aggregate for storage on-site.
One of the challenges on this project was the removal of the roofing and floor tile, which both contained asbestos. The task of soft-stripping these elements is often done by hand to avoid producing excessive dust, but to mitigate potential worker exposure to asbestos fibers, the company employed heavy equipment and a new specialized dust control design from BossTek. Using equipment instead of manpower for demolition and dust suppression improves safety and drastically reduces the amount of time needed for internal stripping.
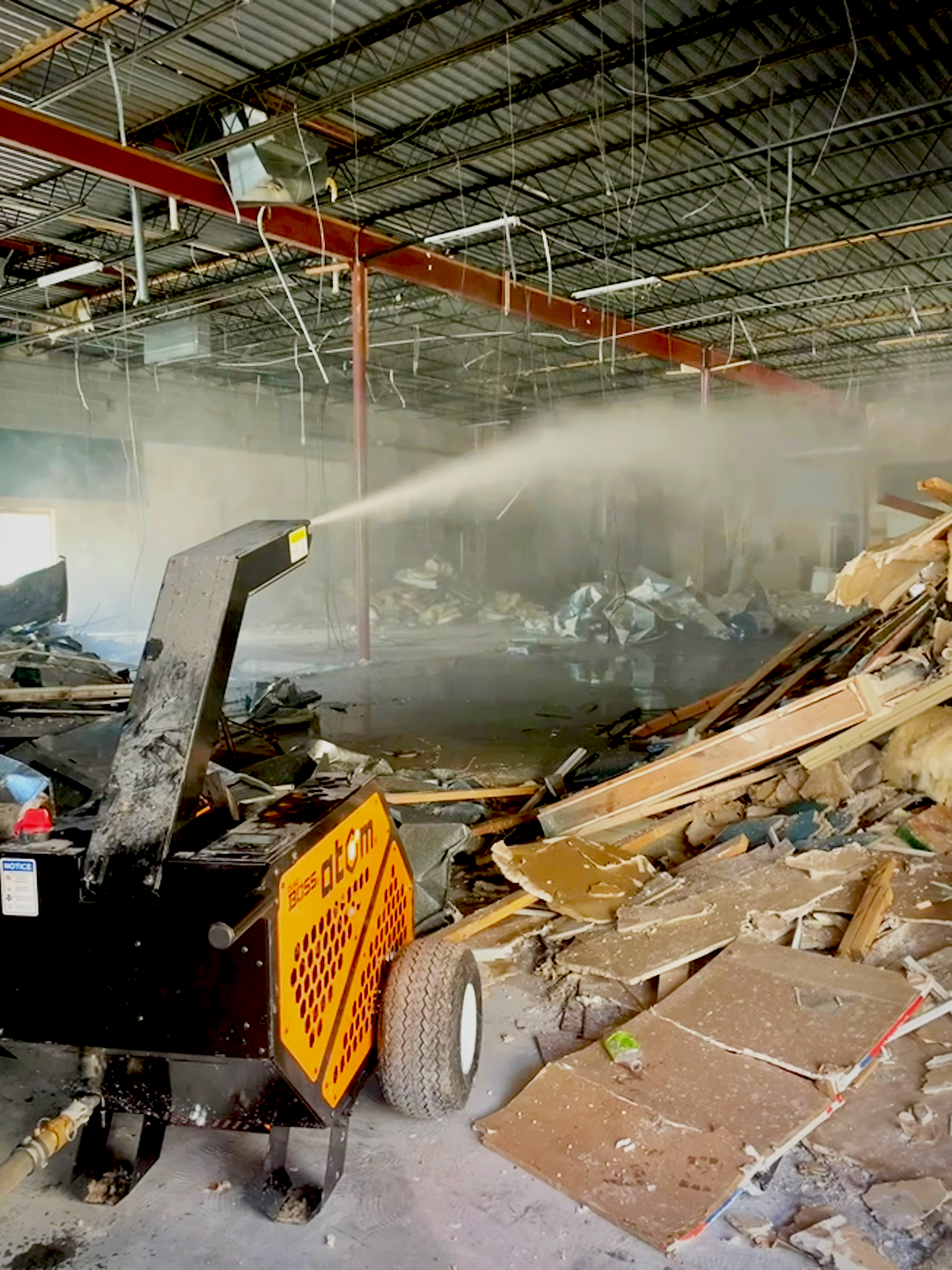
Ensuring that toxic dust doesn’t leave the site is the priority for operators.
Since the Kingsmill project featured tight areas that had to be addressed with precision, the DustBoss Atom was chosen for its ability to produce a highly pressurized water stream that fractures into a fine mist that can be directed right to the source of dust. Using its oscillating head, the compact unit delivers both airborne and surface suppression using a fraction of the water volume of manual spraying, helping to minimize oversaturation and runoff.
A standard hand-held 3/4 inch hose attached to a hydrant generally delivers up to 22 gpm of water. Instead of relying on water pressure, the Atom uses a 1-inch hose attachment from a water source running to a pump powered by a 9.1 HP diesel engine. The increase in pressure from the pump rather than relying on pressure from the hydrant means the design uses only 7 gpm. This greatly reduces wastewater runoff and the amount of standing water in the area, allowing the machine to be distant from the water source and still deliver superior dust control.
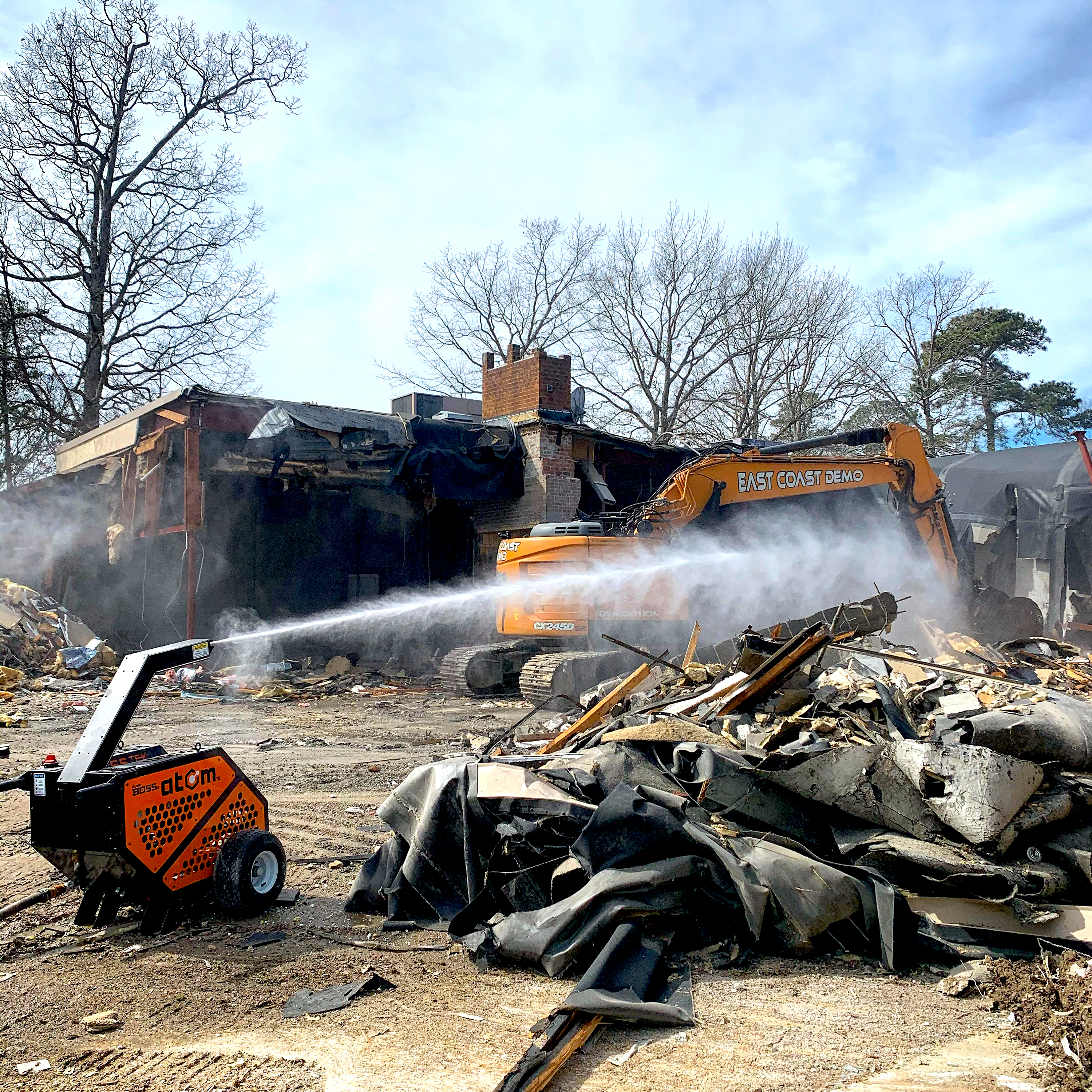
The DustBoss Atom™ controls dust on storage piles during the separation process for recycling.
With a throw of 100 feet, the unit’s 0-65 degree vertical adjustment and 100 degree maximum oscillation range increase the coverage area to 6,100 square feet. Using the handheld remote control, operators can set the oscillation range from the cab of their rig or at a safe distance from the demolition zone.
“A single worker was able to wheel the Atom around by hand, place it, determine the optimum settings and go do something else,” Webb says. “The versatility is great because if we need dust control in another building or on the storage piles, we can get the unit there quickly, turn it on and walk away. The labor savings alone makes it worth the money, but the safety and ease of use are huge benefits.”
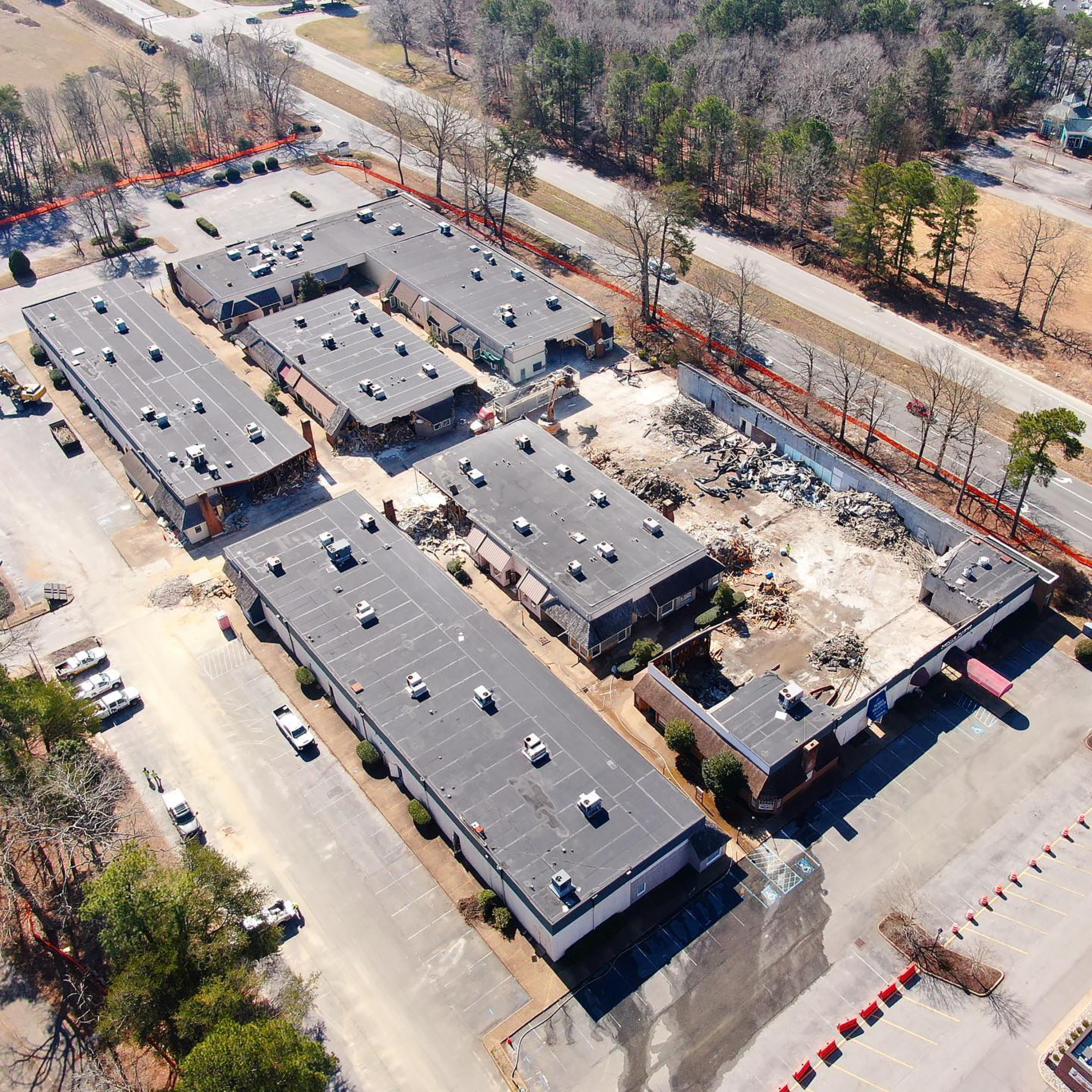
Aerial photos show East Coast Demolition’s methodical process of clearing and sequestering material.
There were some clear advantages to having precision dust control. One is that workers can stay protected in enclosed cabs and change the Atom’s settings with a remote control. Another is the dust’s effect on equipment. In the past, workers performing demolition inside structures had to clean the excessive buildup of dust out of equipment air intakes and radiators to prevent engine breakdowns. Since dust is addressed at the point of emission, this activity is reduced considerably, saving maintenance time and protecting valuable equipment.
Result
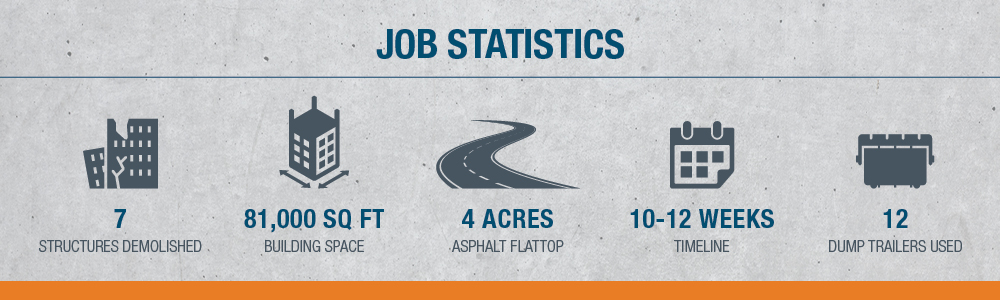
There have been zero dust-related complaints from neighbors and local businesses. This has had a positive impact on the general contractor’s impression — as well as the local environmental inspector’s assessment — of East Coast Demolition.
“From a perception standpoint, when the public and the city observe these DustBoss units in operation, they are immediately more at ease seeing that the dust is being properly contained,” Webb says. “From a business perspective, general contractors know we have the equipment, safety and compliance measures in place to do the job properly.”
By having a versatile hands-free dust control unit, sites are safer and more compliant, while reducing the cost of operation. The compact, diesel-powered DustBoss Atom takes up little room, is useful on any site and is easily maneuverable by a single worker on flat surfaces.
“It was great working with the BossTek team to get us exactly the machine we needed to do the job right,” Webb says. “This equipment has actually helped us capture new business. That’s how much value they bring to our company.”